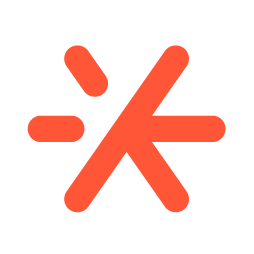
Dans l’industrie, chaque minute d’arrêt non planifié coûte cher. Entre les pertes de production, les coûts de réparation en urgence et l’impact sur la supply chain, une panne peut vite devenir un cauchemar pour les entreprises. Pour éviter ces interruptions et optimiser la durée de vie des équipements, la maintenance prédictive s’impose comme une solution incontournable.
Mais comment anticiper les défaillances avant qu’elles ne surviennent ? C’est là qu’intervient l’ERP. Couplé à l’intelligence artificielle (IA) et aux capteurs IIoT (Industrial Internet of Things), un ERP moderne permet de détecter les signaux faibles annonçant une panne et de planifier des interventions avant qu’un problème ne perturbe la production.
Dans cet article, nous verrons comment un ERP intégré aux nouvelles technologies transforme la maintenance industrielle et pourquoi il est un levier stratégique pour les entreprises cherchant à optimiser leurs actifs.
Traditionnellement, l’entretien des équipements repose sur deux approches :
La maintenance prédictive, elle, repose sur l’analyse en temps réel des données issues des machines pour anticiper les pannes et optimiser les interventions. Résultat : moins de temps d’arrêt, des coûts maîtrisés et une meilleure performance globale.
L’ERP joue un rôle clé dans cette transformation. En centralisant et en analysant les données issues des équipements, il permet aux entreprises d’adopter une gestion proactive des actifs. Mais comment fonctionne concrètement cette intégration ?
L’ERP est le socle sur lequel reposent les stratégies de maintenance modernes. En l’associant à des capteurs IIoT et à l’IA, les entreprises peuvent suivre en temps réel l’état de leurs équipements et détecter les signes annonciateurs d’une défaillance. Voici les étapes clés de ce processus :
Les capteurs installés sur les équipements surveillent en continu des paramètres critiques :
Ces données sont ensuite envoyées directement dans l’ERP.
L’intelligence artificielle analyse les données collectées pour identifier des tendances ou des écarts par rapport aux comportements normaux. Par exemple, une augmentation progressive des vibrations sur un moteur peut signaler une usure prématurée.
Dès qu’une anomalie est détectée, l’ERP génère automatiquement une alerte et propose une action corrective. Les équipes de maintenance reçoivent des recommandations sur la meilleure période pour intervenir, en évitant les périodes de forte production.
L’ERP permet aussi de gérer l’inventaire des pièces détachées et de s’assurer que les bonnes ressources sont disponibles au bon moment. Plus besoin d’acheter des pièces en urgence ou de mobiliser des techniciens pour une panne imprévue.
Tous les ERP ne sont pas conçus pour gérer la maintenance prédictive. Il est essentiel de choisir une solution capable d’intégrer et d’analyser les données issues des capteurs industriels.
Sans données, pas d’analyse possible ! Il est donc indispensable d’équiper les machines critiques avec des capteurs IIoT capables de collecter des données en temps réel.
L’IA et l’analyse de données nécessitent une montée en compétences des équipes de maintenance. Un accompagnement est souvent nécessaire pour tirer pleinement parti des outils prédictifs.
Une approche prédictive ne se limite pas aux équipes de maintenance. Elle doit être intégrée à la stratégie globale de gestion des actifs pour maximiser son impact sur la performance industrielle.
L’association d’un ERP avec l’IA et l’IIoT marque un tournant majeur pour l’industrie. Grâce à cette synergie, les entreprises peuvent passer d’une maintenance réactive à une maintenance proactive, optimisant ainsi leur productivité et réduisant les coûts.
Investir dans une solution ERP capable d’intégrer la maintenance prédictive, c’est faire le choix d’une gestion intelligente des actifs, plus efficace et plus rentable à long terme.